Falling film evaporator are designed to minimize fouling, a common issue in many evaporator systems. Fouling occurs when solids or precipitates in the liquid being processed deposit on the heat transfer surfaces (typically tubes or plates) and reduce heat transfer efficiency. In a falling film evaporator, several design features and operational aspects contribute to fouling reduction:
Thin Liquid Film: Falling film evaporators operate by creating a thin, uniform film of liquid flowing down the heated surface. The thin film minimizes the residence time of the liquid on the heat transfer surface, reducing the chances of fouling. When the liquid film is thin, any solids or impurities in the liquid are less likely to settle and accumulate on the surface.
High Velocity Flow: The liquid film flows down the heating surface at a relatively high velocity. This continuous movement helps prevent the buildup of fouling deposits. The velocity can be adjusted to suit the specific characteristics of the liquid being processed.
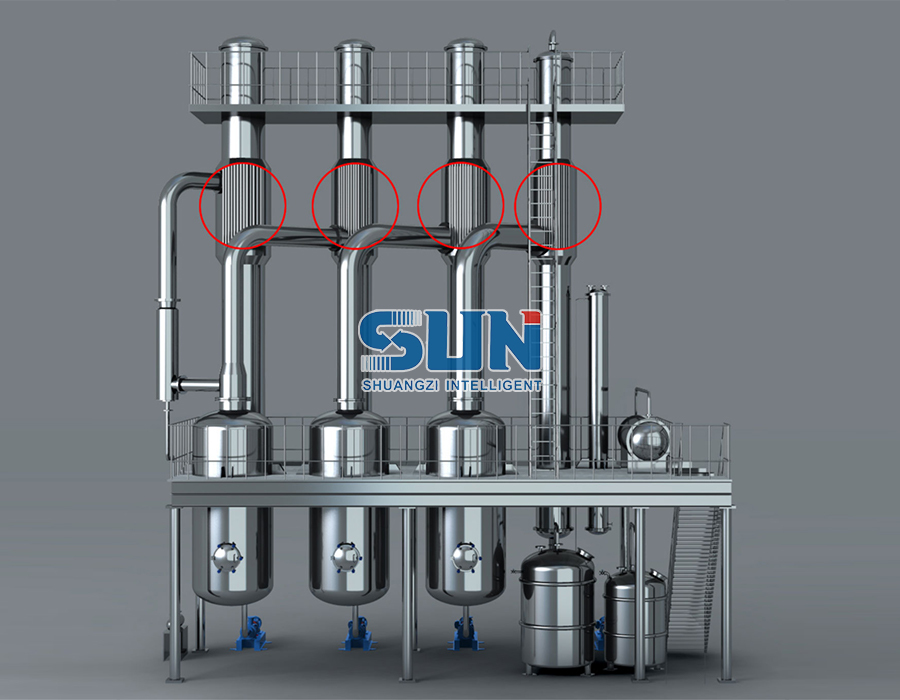
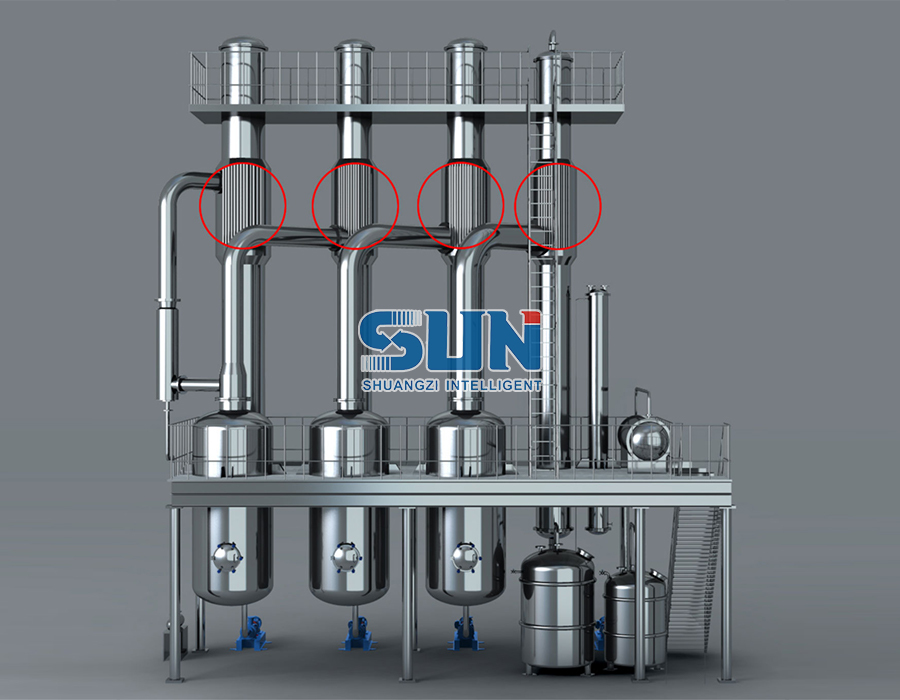
Turbulence: The falling liquid film is inherently turbulent, which enhances heat transfer and helps dislodge any potential fouling deposits. Turbulence promotes mixing and prevents stagnant regions that are conducive to fouling.
Short Residence Time: Falling film evaporators are designed for rapid evaporation and have a short residence time for the liquid on the heated surface. This limited exposure to heat reduces the likelihood of fouling, especially for heat-sensitive materials that can degrade at elevated temperatures.
Anti-fouling Design: Some falling film evaporators incorporate features to minimize fouling. For example, the heating tubes or plates may have special surface treatments or textures that discourage fouling by preventing the adhesion of solids.
Efficient Heat Transfer: Falling film evaporators are efficient at transferring heat to the liquid. This means that the liquid is heated quickly, minimizing the time it spends on the heated surface, which reduces the opportunity for fouling.
Regular Cleaning: While falling film evaporators are designed to minimize fouling, periodic maintenance and cleaning are still necessary. Regular cleaning routines can help prevent the accumulation of fouling deposits over time.
Optimized Process Parameters: Proper control of process parameters such as temperature, flow rate, and vacuum level is essential to minimize fouling. By maintaining optimal conditions, fouling tendencies can be reduced.
Despite these advantages, fouling can still occur in falling film evaporators, especially when processing liquids with high concentrations of solids or when dealing with challenging materials. In such cases, additional measures like mechanical cleaning systems or chemical cleaning solutions may be employed to address fouling and ensure the continued efficiency of the evaporator.